Category

Contact
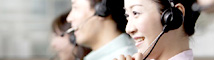
Tel: ( 86) 755-26996606
Fax: ( 86) 755-26007653
E-mail: rosemary@ussharp.com
Woods-tiger@ussharp.com
Web site: www.ussharp.com
Address: Floor 4, Jinhui Building, Nanhai Road, Nanshan District, ShenZhen

News
A good example of material-driven tooling development is the growing selection of tools for machining aluminum. In the quest for fuel efficiency, the use of aluminum in vehicle manufacturing is constantly increasing. While in 1980 aluminum made up approximately 3 percent (representing 34 kg/75 lbs) of a typical midsize car, that proportion had risen to about 5 percent by 1990. Forecasts for cars of the future indicate that aluminum usage will rise to between 10 percent and 20 percent of the total vehicle weight, with engine blocks, cylinder heads, and housings being major contributors to consumption.
Although uncoated carbides and polycrystalline diamond tools presently dominate the turning, milling and drilling of aluminum/silicon alloys, the increasing aluminum usage has hastened the development of thinfilm diamondcoated carbide cutting tools (Figure 1, at left). Diamondcoated tools offer wear resistance comparable to polycrystalline diamond materials, while also providing multiple insert edges and the ability to support complex chipcontrol geometries. The dual advantages of high wear resistance and geometric flexibility make diamondcoated tools excellent candidates to replace uncoated carbides as well as expensive PCD cutting tools. Diamond coating is being extended to more difficult tool geometries including drills and end mills. And, for hypoeutectic aluminum as well as magnesium alloys, titanium diboride (TiB2) coatings applied by the physical vapor deposition (PVD) process offer productivity advantages
Related information
- 2012-12-23Efficiency of Milling Cutters
- 2012-11-11Turning Machines
- 2012-10-16Ceramics For Difficult Materials
- 2012-08-07PVD:Sharp for Steel
- 2012-07-15New Irons In The Fire
